Как се обработват високопрецизните части
2023-09-22
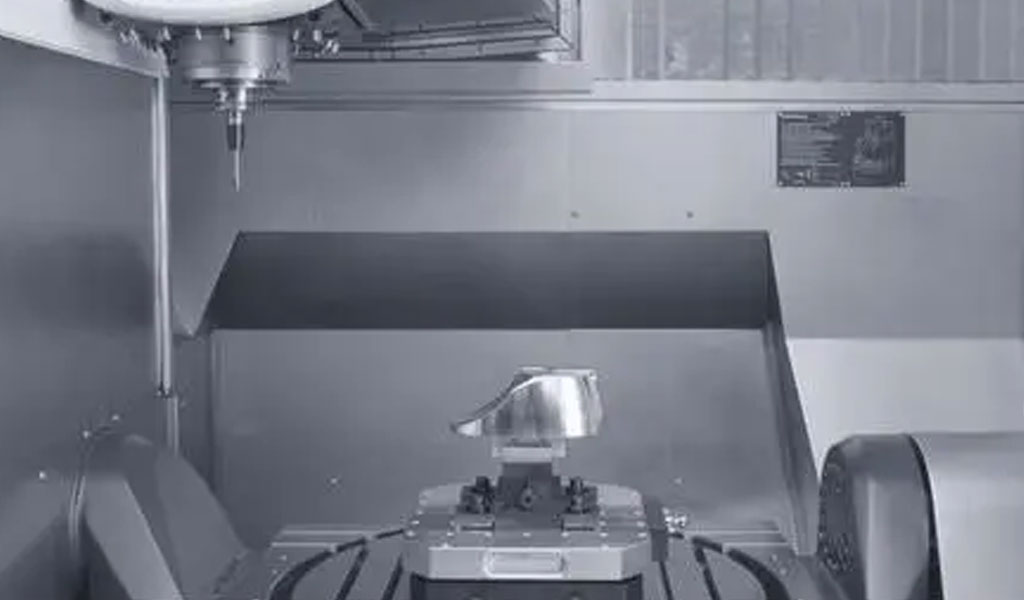
Разбиране на прецизната обработка
Прецизната машинна обработка е крайъгълен камък на модерното производство, отговорен за производството на сложни и точни компоненти, използвани в широк спектър от индустрии. За да разберем напълно значението му, нека проучим основните концепции на прецизната машинна обработка, неговата жизненоважна роля в различни сектори и историческото пътуване, довело до сегашното му състояние на съвършенство.A. Какво е прецизна обработка?
Прецизната машинна обработка се отнася до набор от производствени процеси, които премахват материал от детайла с висока степен на точност и контрол, което води до фино изработени компоненти с тесни допуски. Този процес трансформира суровини, като метали, пластмаси или керамика, в прецизни части, които отговарят на точните спецификации. Основните характеристики на прецизната обработка включват:- Точност: Прецизната машинна обработка гарантира, че крайният продукт отговаря точно на предвидения дизайн, с минимално отклонение.
- Тесни толеранси: Позволява производството на части с изключително тесни допуски, което означава, че готовите компоненти се придържат точно към определени измервания.
- Превъзходно покритие на повърхността: Прецизната машинна обработка осигурява изключителна повърхностна обработка, често елиминирайки необходимостта от допълнителни довършителни процеси.
- Комплексни геометрии: Може да създава сложни форми, контури и характеристики, което го прави незаменим при производството на компоненти със сложен дизайн.
- Повторяемост: Прецизност процес на обработкаes са много повторяеми, осигурявайки постоянно качество в множество части.
- Гъвкавост: Може да се прилага към широка гама от материали, което го прави подходящ за различни индустрии.
Б. Значение на прецизната обработка
Прецизната машинна обработка има огромно значение в няколко критични индустрии, оказвайки влияние върху различни аспекти от нашето ежедневие. Ето някои убедителни причини за важността му:- Аерокосмическа индустрия: В аерокосмическия сектор прецизната машинна обработка е незаменима за изработване на компоненти, които издържат на екстремни условия. Самолетни двигатели, кацане механизъм, а структурните елементи разчитат на прецизно обработени части за безопасност и производителност.
- Медицински изделия: Медицински устройства като хирургически инструменти, протези и имплантируеми устройства изискват прецизна обработка за биосъвместимост, точност и безопасност на пациента.
- Автомобилен сектор: Прецизно обработените части са от съществено значение за автомобилната индустрия, за да гарантират надеждността и ефективността на превозните средства. Компоненти като части на двигателя, трансмисионни системи и спирачни механизми разчитат на прецизна машинна обработка.
- Електроника и полупроводници: Прецизната машинна обработка е ключова в производството на микроелектронни компоненти и полупроводникови устройства, където малките допуски са наложителни за функционалността.
- Енергиен сектор: Енергийната индустрия разчита на прецизна машинна обработка за производството на критични части, използвани в производството на електроенергия, включително турбини, генератори и трансмисионни компоненти.
- Изработка на инструменти и матрици: Прецизната машинна обработка е от решаващо значение при производството на инструменти и матрици, които от своя страна се използват за създаване на безброй други продукти.
- Потребителска електроника: Производството на смартфони, лаптопи и друга потребителска електроника се възползва от прецизната машинна обработка, за да осигури елегантен дизайн и оптимална функционалност.
- Научни изследвания и разработки: Изследователите и учените разчитат на прецизно обработени компоненти за експерименти, прототипи и лабораторно оборудване.
В. Историческа перспектива
Пътуването на прецизната машинна обработка води началото си от древните цивилизации, където квалифицирани занаятчии са използвали елементарни инструменти за оформяне на материали. Прецизността, постигната в онези времена обаче, беше ограничена в сравнение със съвременните стандарти.- Ранна прецизна обработка: Индустриалната революция от 18-ти и 19-ти век бележи ключов период в развитието на прецизната обработка. Изобретяването на машинни инструменти, като стругове и фрезови машини, направи революция в производството, като позволи по-голяма точност и последователност.
- Втората световна война: Прецизната машинна обработка изигра централна роля през Втората световна война, тъй като беше от съществено значение за производството на военно оборудване с необходимата прецизност и еднаквост. Тази ера е свидетел на напредък в техниките за обработка и появата на нови материали.
- Следвоенен напредък: Следвоенният период видя скок в технологичните иновации, включително използването на машини с компютърно цифрово управление (CNC). CNC машинна обработка позволяват автоматизирани и високо прецизни операции, поставяйки началото на нова ера в производството.
- Дигиталната ера: Интегрирането на компютри и софтуер в процесите на обработка допълнително повиши прецизната обработка. Съвременните CNC машини могат да изпълняват сложни операции с несравнима точност, което ги прави незаменими в днешния производствен пейзаж.
Материали и тяхното значение
Материалите са в основата на прецизната машинна обработка и изборът на правилния материал играе ключова роля в производството на детайли с висока точност. В този раздел ще разгледаме значението на избора на подходящите материали, ще разберем значението на свойствата на материала и ще проучим различните фактори, които влияят на обработваемостта.A. Избор на материали
Изборът на материали при прецизната обработка е критично решение, което пряко влияе върху производителността, издръжливостта и функционалността на крайния продукт. Производителите трябва да вземат предвид няколко фактора при избора на материали:- Пригодност на материала: Материалът трябва да е подходящ за предвиденото приложение. Различните индустрии и приложения имат различни изисквания, като температурна устойчивост, устойчивост на корозия и електрическа проводимост.
- Механични свойства: Механични свойства като якост на опън, твърдост и пластичност са от решаващо значение. Например в космическото пространство за структурни компоненти се предпочитат материали с висока якост на опън.
- Топлинни свойства: Някои приложения изискват материали с отлична топлопроводимост или устойчивост на високи температури. Това е особено важно в индустрии като производство на електроенергия и електроника.
- Устойчивост на корозия: В среди, където корозията е проблем, се предпочитат материали с висока устойчивост на корозия, като неръждаема стомана или титан.
- Съображения за тегло: Индустрии като автомобилната и космическата често дават приоритет на леки материали като алуминий или композити от въглеродни влакна, за да намалят разхода на гориво и да подобрят производителността.
- Ограничения на разходите: Цената е важен фактор при избора на материал. Материалите с висока производителност могат да бъдат скъпи, така че производителите трябва да намерят баланс между производителност и рентабилност.
- Нормативно съответствие: В отрасли като здравеопазването материалите трябва да отговарят на строги регулаторни стандарти за биосъвместимост и безопасност.
- Наличност: Наличието на материали и техните източници също оказват влияние върху избора. Някои специализирани сплави или композити може да са с ограничена наличност.
Б. Свойства на материала
Разбирането на свойствата на материалите е от решаващо значение за прецизната обработка. Ето някои ключови свойства на материала и тяхното значение:- Издръжливост на опън: Якостта на опън измерва способността на материала да издържи сила на теглене, без да се счупи. Той е от съществено значение за структурни компоненти и части, подложени на механично натоварване.
- Твърдост: Твърдостта показва устойчивостта на материала на деформация и износване. Твърдите материали са подходящи за режещи инструменти, докато по-меките материали могат да бъдат предпочитани за определени приложения, като уплътнения.
- еластичност: Пластичността се отнася до способността на материала да се деформира, без да се счупи, когато е подложен на напрежение на опън. Пластичните материали са по-лесни за оформяне, но може да не са подходящи за приложения, изискващи твърдост.
- Топлопроводимост: Материалите с висока топлопроводимост ефективно разсейват топлината. Това свойство е жизненоважно в приложения, където контролът на температурата е критичен.
- Електропроводимост: Електрическата проводимост е от съществено значение в електрониката и електрическите компоненти, където материалите трябва да улесняват потока на електричество.
- Магнитни свойства: Магнитните свойства са важни в индустрии като електромагнетика и електроника, където може да се наложи материалите да бъдат феромагнитни или немагнитни.
- Химична устойчивост: Материалите трябва да са устойчиви на химическа корозия в среди, където са изложени на киселини, основи или други корозивни вещества.
C. Фактори за обработваемост
Обработваемостта се отнася до лекотата, с която даден материал може да бъде обработен, нарязан или оформен. Той се влияе от различни фактори, включително:- Твърдост на материала: По-меките материали обикновено се обработват по-лесно, докато по-твърдите материали може да изискват специализирани инструменти и техники.
- Образуване на чипове: Образуването и изхвърлянето на стърготини по време на машинната обработка влияят върху ефективността на процеса и покритието на повърхността.
- Износване на инструменти: Различните материали могат да причинят различна степен на износване на инструмента, оказвайки влияние върху скоростта и цената на обработка.
- Охлаждаща течност и смазване: Подходящата охлаждаща течност и смазка са от съществено значение за намаляване на триенето, топлината и износването на инструмента по време на обработка.
- Рязане на скоростта: Скоростта, с която режещият инструмент се движи през материала, влияе както върху производителността, така и върху качеството на обработваната повърхност.
- Материал на инструмента: Изборът на материал за режещ инструмент, като карбид или бързорежеща стомана, зависи от материала, който се обработва.
- Параметри на рязане: Регулирането на параметри на рязане като скорост на подаване и дълбочина на рязане може да оптимизира процеса на обработка за конкретни материали.
Машини за прецизна обработка
Машинните инструменти са сърцето на прецизната машинна обработка, което позволява трансформирането на суровини във високо прецизни части. В този раздел ще разгледаме четири ключови типа машинни инструменти, използвани при прецизна обработка: CNC обработващи центри, стругови машини, шлифовъчни машини и EDM (обработка с електроразряд). Всяка от тези машини играе уникална роля в производството на прецизни компоненти.A. CNC обработващи центрове
CNC (компютърно цифрово управление) обработващи центрове са универсални и широко използвани в прецизната обработка. Те са автоматизирани системи, които контролират движението на режещите инструменти и детайлите с изключителна прецизност. Ето общ преглед на обработващите центри с ЦПУ и тяхното значение:- Гъвкавост: CNC обработващите центрове могат да извършват различни операции по обработка, включително фрезоване, пробиване и нарязване на резби. Тази гъвкавост позволява производството на сложни части с множество функции.
- Висока прецизност: Компютъризираното управление на CNC машини гарантира прецизно позициониране на инструмента и постоянни резултати, което ги прави идеални за детайли с тесни допуски.
- Автоматизация: CNC обработващите центрове могат да работят непрекъснато, с минимална човешка намеса. Тази автоматизация повишава ефективността и намалява риска от грешки.
- Комплексни геометрии: Те са отлични при обработката на сложни форми и контури, което ги прави подходящи за индустрии като космическата индустрия, където сложните компоненти са често срещани.
- Повтарящи се резултати: CNC машините предлагат отлична повторяемост, като гарантират, че всяка произведена част отговаря на точните спецификации на дизайна.
- Намалено време за настройка: Обработващите центрове с ЦПУ могат да бъдат програмирани да превключват бързо между различни задачи, минимизирайки времето за настройка и повишавайки ефективността на производството.
Б. Стругови машини
Машините за струговане се използват за създаване на цилиндрични части чрез въртене на детайла, докато режещ инструмент премахва материала от външната му повърхност. Те са от съществено значение за производството валs, щифтове и други компоненти с ротационна симетрия. Ключовите моменти за струговащите машини включват:- Цилиндрични части: Машините за струговане са специализирани в производството на цилиндрични или тръбни компоненти, включително такива с резби или сложни канали.
- Високи скорости: Те работят при високи скорости, което ги прави подходящи за части, които изискват гладко и точно покритие.
- Работа с една ос: Повечето машини за струговане са едноосни, фокусирани върху оформянето на външната повърхност на детайла.
- Ефективно за масово производство: Струговането е високоефективно за детайли за масово производство с минимални материални отпадъци.
- Стругови машини: Струговете с ръчно и CNC управление са често използвани машини за струговане, предлагащи набор от възможности.
C. Шлифовъчни машини
Шлифовъчните машини са предназначени за прецизна повърхностна обработка и оформяне на твърди или абразивни материали. Те са от решаващо значение за постигане на изключително строги допуски и превъзходно покритие на повърхността. Ето защо шлифовъчните машини са важни:- Прецизност на микронно ниво: Шлифовъчните машини могат да постигнат прецизност на микронно ниво, което ги прави от съществено значение за приложения, които изискват най-високо ниво на точност.
- Отстраняване на материал: Отстраняват материала чрез абразия, като позволяват коригиране на повърхностните несъвършенства и постигане на изключителна гладкост.
- Заточване на инструменти и ножове: Освен повърхностно шлайфане има специализирани шлифовъчни машини за заточване на режещи инструменти и изработване на прецизни профили.
- Разнообразие от методи на смилане: Различни видове шлифовъчни машини, включително повърхностни шлайфове, цилиндрични шлифовъчни машини и безцентрови шлифовъчни машини, отговарят на различни нужди от машинна обработка.
- Втвърдени материали: Шлифоването е особено подходящо за закалени материали като инструментална стомана и керамика, където традиционните методи на обработка може да са неефективни.
D. EDM (Електроразрядна обработка)
EDM или Electrical Discharge Machining е нетрадиционен процес на обработка, който използва електрически разряди за оформяне на материали. Той е идеален за създаване на сложни и деликатни части, където традиционните режещи инструменти могат да причинят повреда. Ключовите аспекти на EDM включват:- Без физически контакт: EDM не включва директен физически контакт между инструмента и детайла, минимизирайки риска от износване на инструмента и повреда на крехки материали.
- Висока прецизност: Може да постигне висока прецизност и качество на повърхността, дори при изключително твърди материали.
- Wire EDM и Sinker EDM: Има два основни типа EDM машини: рязане на тел EDM, който използва теленен електрод, и потъващ EDM, който използва оформен електрод.
- Сложни форми: EDM може да произвежда сложни форми, като щанци и форми, със сложни детайли и фини характеристики.
- Термично засегната зона: Тъй като EDM не генерира топлина в детайла, той е подходящ за чувствителни на топлина материали като авиационни сплави.
- Бавен процес: EDM е сравнително бавен в сравнение с други методи на обработка, което го прави най-подходящ за задачи с ниско количество и висока точност.
Режещи инструменти и инструменти
Режещите инструменти са в челните редици на прецизната машинна обработка, служейки като инструменти, които оформят и трансформират суровините във високо прецизни части. В този раздел ще разгледаме различните видове режещи инструменти, значението на покритията на инструментите и факторите, влияещи върху живота и износването на инструмента.А. Видове режещи инструменти
Прецизната обработка разчита на разнообразна гама от режещи инструменти, всеки от които е проектиран за специфични задачи и материали. Изборът на режещ инструмент значително влияе върху ефективността и точността на процеса на обработка. Ето някои често срещани видове режещи инструменти:- Край мелници: Крайните фрези са универсални инструменти, използвани за фрезови операции. Те имат множество режещи ръбове и могат да отстраняват материал от детайла по различни начини, включително облицовка, контуриране и прорязване.
- Сонди: Бормашините са предназначени за създаване на отвори в детайли. Те се предлагат в различни форми, включително спирални свредла, централни свредла и сменяеми свредла.
- Обръщане на вмъквания: Те се използват в стругови машини за оформяне на цилиндрични части. Вложките за струговане се предлагат в различни форми и материали, за да отговарят на различни приложения.
- Фрези: Фрезите се предлагат в различни форми, като челни мелници, топкови мелници и фрезови фрези, и се използват в фрезови машини за създаване на различни елементи върху детайла.
- райбери: Райберите се използват за довършване и оразмеряване на предварително пробити отвори до точни размери. Осигуряват гладки и точни повърхности на отворите.
- Кранове и матрици: Тези режещи инструменти се използват за резбови операции. Метчовете създават вътрешни резби, докато матриците създават външни резби.
- Шлифовъчни колела: Шлифовъчните дискове са абразивни инструменти, използвани за прецизно шлифоване на повърхности. Предлагат се в различни абразивни материали и размери на зърното.
- Брошки: Протяжките са специализирани инструменти, използвани за рязане на вътрешни и външни форми и профили, като шпонкови канали и шлици.
- Зенкери и зенкери: Тези инструменти се използват за създаване на вдлъбнатини или фаски около дупки за закопчалкаs.
- Скучни барове: Пробивните пръти се използват при сондажни операции за уголемяване на съществуващи отвори с прецизност.
Б. Покрития за инструменти
Покритията на инструментите са тънки слоеве от материал, нанесени върху режещите инструменти за подобряване на тяхната производителност и издръжливост. Тези покрития предлагат няколко предимства:- Намалено триене: Покрития като титанов нитрид (TiN) и титанов карбонитрид (TiCN) намаляват триенето между инструмента и детайла, което води до по-гладко рязане и по-дълъг живот на инструмента.
- Повишена твърдост: Покритията повишават твърдостта на повърхността на инструмента, което го прави по-устойчив на износване и удължава живота на инструмента.
- Подобрена устойчивост на топлина: Покритията могат да издържат на високи температури, генерирани по време на обработката, намалявайки свързаното с топлината износване на инструмента и увеличавайки скоростите на рязане.
- Свойства против натрупване: Някои покрития имат антиадхезионни свойства, предотвратявайки натрупването на материал върху режещите ръбове на инструмента.
- Повишена смазваща способност: Инструментите с покритие имат подобрена смазваща способност, намалявайки необходимостта от прекомерна охлаждаща течност и подобрявайки евакуацията на стружките.
C. Живот и износване на инструмента
Разбирането на живота и износването на инструмента е от решаващо значение за оптимизиране на процесите на обработка и минимизиране на производствените разходи. Животът на инструмента се отнася до продължителността, през която режещият инструмент остава ефективен, преди да изисква подмяна или възстановяване. Няколко фактора влияят върху живота и износването на инструмента:- Рязане на скоростта: По-високите скорости на рязане могат да доведат до повишено износване на инструмента поради по-високите температури, генерирани по време на обработката. Правилният избор на скорости на рязане е от съществено значение за балансиране на живота на инструмента и производителността.
- Скорост на подаване: Скоростта, с която режещият инструмент напредва в детайла, влияе върху износването на инструмента. Високите скорости на подаване могат да ускорят износването, докато по-ниските скорости на подаване могат да удължат живота на инструмента.
- Дълбочина на рязане: Дълбочината на рязане влияе върху количеството материал, отстранен за едно преминаване. По-дълбоките срезове могат да увеличат износването на инструмента, така че оптимизирането на дълбочината е от решаващо значение.
- Твърдост на материала: Рязането на твърди материали може да ускори износването на инструмента. Специализирани инструменти и покрития се използват за ефективна обработка на твърди материали.
- Охлаждаща течност и смазване: Подходящата охлаждаща течност и смазка помагат за разсейване на топлината и намаляване на триенето, удължавайки живота на инструмента.
- Материал на инструмента: Материалът, от който е направен режещият инструмент, влияе върху неговата устойчивост на износване. Материали като карбид и керамика предлагат отлична устойчивост на износване.
- Геометрия на инструмента: Геометрията на режещия инструмент, включително наклонен ъгъл, релефен ъгъл и конструкция на стружколома, играе важна роля в моделите на износване.
- Материал на детайла: Видът на обработвания материал влияе върху износването на инструмента. Абразивните материали могат да доведат до по-бързо износване на инструмента.
Процеси на прецизна обработка
Процесите на прецизна обработка са методите, чрез които суровините се трансформират във високо прецизни детайли с тесни допуски и изключителна повърхностна обработка. В този раздел ще разгледаме пет ключови процеса на прецизна обработка: струговане, фрезоване, пробиване, шлайфане и електроерозионна обработка (EDM). Всеки от тези процеси служи за уникална цел и се използва въз основа на специфичните изисквания на детайла.А. Обръщане
Струговането е процес на обработка, използван предимно за оформяне на цилиндрични части. Това включва въртене на детайла, докато режещ инструмент с една точка премахва материала от външната повърхност. Ето основните аспекти на обръщането:- Цилиндрични части: Струговането е идеално за производство на цилиндрични компоненти като валове, щифтове и втулки.
- Ротационна симетрия: Той е много подходящ за части, изискващи ротационна симетрия, тъй като детайлът се върти на струг, докато режещият инструмент го оформя.
- Различни операции: Струговането може да извършва различни операции, включително облицоване, завъртане (намаляване на диаметъра), завъртане на конус и нарязване на резба.
- Рязане в една точка: Единичен режещ инструмент премахва материала с непрекъснато движение, което води до ефективно отстраняване на материала.
- Стругови машини: Както ръчните, така и управляваните с ЦПУ стругове обикновено се използват за струговане.
Б. Фрезоване
Фрезоването е универсален процес на прецизна обработка, който използва многоточкови режещи инструменти за отстраняване на материал от детайла. Той е много подходящ за създаване на широка гама от форми и характеристики. Ключовите аспекти на фрезоването включват:- Гъвкавост: Фрезоването може да произвежда плоски повърхности, прорези, джобове и сложни контури. Използва се както за 2D, така и за 3D обработка.
- Многоточково рязане: Множество режещи ръбове на инструмента взаимодействат с детайла едновременно, което позволява ефективно отстраняване на материала.
- Видове фрезоване: Фрезоването може да се извърши с помощта на различни видове фрези, включително челни мелници, челни мелници и топкови мелници.
- CNC обработващи центрове: CNC управляваните фрезови машини предлагат прецизен контрол върху движението на инструмента и се използват широко в съвременната обработка.
- Високи скорости: Фрезоването може да се извършва при високи скорости, което позволява ефективно производство.
В. Сондиране
Пробиването е процес на прецизна обработка, използван за създаване на отвори в детайлите. Това е основна операция в различни индустрии. Ключовите аспекти на сондирането включват:- Създаване на дупка: Пробивните машини използват специализирани инструменти, наречени свредла, за отстраняване на материал и създаване на дупки с определени диаметри.
- Видове свредла: Предлагат се различни видове свредла, включително спирални свредла, централни свредла и сменяеми свредла, всяко от които е проектирано за специфични приложения.
- Точност: Прецизното позициониране и подравняване са от съществено значение при пробиването, за да се гарантира, че отворите са създадени с точност.
- Скорост и скорост на подаване: Параметри на пробиване като скорост на въртене и скорост на подаване са критични за постигане на желаните размери на отвора.
- Охлаждаща течност и смазване: Подходяща охлаждаща течност и смазка се използват за разсейване на топлината и намаляване на триенето по време на пробиване.
Г. Смилане
Шлифоването е процес на прецизна обработка, който използва абразивни колела за отстраняване на материала и постигане на изключително строги допуски и повърхностни покрития. Основните аспекти на смилането включват:- Изключителна прецизност: Шлифоването може да постигне прецизност на микронно ниво, което го прави идеално за приложения, изискващи най-висока точност.
- Обработка на повърхността: Постига превъзходно покритие на повърхността, като често елиминира необходимостта от допълнителни довършителни процеси.
- материали: Шлифоването е подходящо за твърди и абразивни материали, включително закалена стомана, керамика и карбиди.
- Разнообразие от методи на смилане: Различни видове шлифовъчни машини, като повърхностни шлифовъчни машини, цилиндрични шлифовъчни машини и безцентрови шлифовъчни машини, отговарят на различни нужди от обработка.
- Антифриз: Подходящата охлаждаща течност е от съществено значение при шлифоването, за да се предотврати прегряване и да се поддържа целостта на диска.
E. Електроерозионна обработка (EDM)
EDM или Electrical Discharge Machining е нетрадиционен процес на прецизна обработка, който използва електрически разряди за отстраняване на материал. Той е особено подходящ за обработка на сложни и сложни форми, както и на твърди и топлоустойчиви материали. Ключовите аспекти на EDM включват:- Безконтактна обработка: EDM не включва директен контакт между инструмента и детайла, намалявайки риска от износване и повреда на инструмента.
- Висока прецизност: EDM може да постигне висока прецизност, което го прави подходящ за приложения, където тесните допуски са от съществено значение.
- Сложни форми: Превъзходен е при обработката на сложни форми, щанци, форми и компоненти с фини детайли.
- Wire EDM и Sinker EDM: Има два основни типа EDM машини: EDM с тел, който използва тел електрод, и EDM с потъващо устройство, който използва оформен електрод.
- Бавен процес: EDM е сравнително бавен в сравнение с други методи на обработка, което го прави най-подходящ за задачи с ниско количество и висока точност.
Допустими отклонения и контрол на качеството
Прецизната машинна обработка изисква щателно внимание към детайлите и строг ангажимент за контрол на качеството, за да се гарантира, че частите отговарят на определените стандарти. В този раздел ще проучим три критични аспекта на контрола на качеството при прецизната обработка: Геометрично оразмеряване и толеранс (GD&T), Статистически контрол на процеса (SPC) и Осигуряване на качеството.A. Геометрично оразмеряване и толеранс (GD&T)
Геометрично оразмеряване и толеранс, често съкратено като GD&T, е система, използвана за дефиниране и съобщаване на допустимите вариации в размера, формата, ориентацията и местоположението на характеристиките на част. GD&T е жизненоважен при прецизната обработка поради следните причини:- Прецизна комуникация: GD&T предоставя стандартизиран език за инженери, дизайнери и машинисти, за да комуникират точно намеренията на дизайна и изискванията за размери.
- Изясняване на толерантността: Помага да се дефинират приемливите вариации в критичните размери, като се гарантира, че всички заинтересовани страни разбират допустимите отклонения.
- Подобрено качество: GD&T насърчава подобреното качество чрез намаляване на двусмислието в спецификациите на дизайна, свеждайки до минимум риска от грешки по време на машинна обработка.
- Ефективност на Разходите: : Ясните GD&T спецификации могат да доведат до намалени производствени разходи, тъй като е по-малко вероятно частите да бъдат бракувани или да изискват преработване поради неразбиране или погрешно тълкуване.
- Комплексна геометрия: Особено полезно е за части със сложна геометрия, като гарантира, че всички характеристики са произведени според желаните спецификации.
B. Статистически контрол на процеса (SPC)
Статистическият контрол на процеса (SPC) е методология за контрол на качеството, която използва статистически техники за наблюдение и контрол на процеса на обработка. SPC е от съществено значение при прецизната обработка поради следните причини:- Мониторинг на процесите: SPC помага да се наблюдават процесите на обработка в реално време, идентифицирайки вариации или отклонения от желаните параметри.
- Ранно откриване на проблеми: Чрез непрекъснато наблюдение на процеса, SPC позволява ранно откриване на проблеми, които биха могли да доведат до части извън спецификациите, намалявайки отпадъците и преработката.
- Вземане на решения, управлявани от данни: SPC разчита на данни и статистически анализ, за да взема информирани решения относно корекциите на процеса, като гарантира, че процесът на обработка остава в приемливи граници.
- Подобрена консистенция: SPC насърчава последователността на процеса и намалява вероятността от производство на несъответстващи части.
- Намален скрап и преработка: Чрез своевременно идентифициране и адресиране на вариациите на процеса, SPC минимизира производството на дефектни части, намалявайки разходите за скрап и преработка.
C. Осигуряване на качеството при прецизна обработка
Осигуряването на качеството при прецизната машинна обработка обхваща цялостен подход за гарантиране, че произведените части отговарят или надвишават определени стандарти за качество. Той включва различни елементи, включително:- Документация на процеса: Подробна документация на процесите на обработка, включително стандартни оперативни процедури (SOP) и работни инструкции, гарантира, че всяка стъпка се изпълнява последователно.
- Проверка и измерване: Строга проверка и измерване с помощта на прецизни инструменти и метрологични техники потвърждават, че частите отговарят на определени толеранси и стандарти за качество.
- Калибровка: Редовното калибриране на машинното оборудване и измервателните инструменти е от съществено значение за поддържане на точност и проследимост.
- Материална проверка: Проверката на свойствата на материала, състава и качеството е от решаващо значение, за да се гарантира, че използваният материал отговаря на изискванията за проектиране.
- Обучение на служителите: Програмите за обучение и развитие на умения за машинисти и персонал за контрол на качеството гарантират, че те са компетентни в своите роли и отговорности.
- Анализ на първопричините: Когато се идентифицират несъответстващи части, се извършва анализ на първопричината, за да се определи източникът на проблема и да се приложат коригиращи действия.
- Непрекъснато Усъвършенстване: Културата на непрекъснато усъвършенстване насърчава иновациите и води до непрекъснати подобрения в процесите на обработка и процедурите за контрол на качеството.
- Обратна връзка с клиентите: Събирането и анализирането на обратната връзка с клиентите помага да се идентифицират области за подобрение и привежда процесите на обработка в съответствие с очакванията на клиентите.
Заключение
A. Изкуството и науката за прецизната обработка
Прецизната машинна обработка стои в пресечната точка на изкуството и науката, където креативността, уменията и иновациите се събират, за да произвеждат високо прецизни части, които движат индустриите и оформят съвременния свят. Това е едновременно форма на изкуство, изискваща майсторството и експертизата на машинистите, които превръщат суровините в произведения на инженерно съвършенство, и наука, която разчита на авангардни технологии, наука за материалите и усъвършенствани процеси за постигане на несравнима прецизност. Пътуването на прецизната машинна обработка ни превежда през разбирането на материалите и техните свойства, овладяването на режещите инструменти и машини и щателния контрол на процесите и допуските. Той обхваща езика на геометричните размери и толерантността, бдителността на статистическия контрол на процеса и ангажимента за осигуряване на качество. Прецизната машинна обработка играе ключова роля в различни индустрии, от космическата и автомобилната до медицинските устройства и електрониката, оформяйки всичко - от самолетни двигатели до изкуствени стави и микрочипове. Позволява създаването на компоненти, които работят с несравнима точност и надеждност, често разширявайки границите на възможното.Б. Последни мисли
Когато приключваме това изследване на прецизната машинна обработка, става ясно, че това поле не е само за създаването на части; става дума за създаване на възможности. Стремежът към прецизност движи иновациите, разширявайки границите на това, което може да се постигне. Независимо дали става въпрос за деликатната изработка, необходима за създаването на сложни зъбни колела на часовника, или за усъвършенстваната технология, необходима за производството на сложни аерокосмически компоненти, прецизната машинна обработка е в основата на всичко това. Бъдещето на прецизната обработка е изпълнено с обещания. Напредъкът в науката за материалите, автоматизацията и цифровите технологии продължават да прекрояват пейзажа. Миниатюризацията, 3D печатът и практиките за устойчиво производство стават все по-видими, откривайки нови хоризонти за индустрията. В свят, в който прецизността има повече значение от всякога, прецизната обработка остава незаменим стълб на съвременното инженерство. Това е свидетелство за човешката изобретателност и нашия непреклонен стремеж към съвършенство във всеки аспект на производството. Тъй като търсенето на по-висока прецизност и по-сложни компоненти нараства, прецизната машинна обработка ще продължи да се развива, посрещайки предизвикателствата на утрешния ден със същата отдаденост и прецизност, които са я определяли от векове.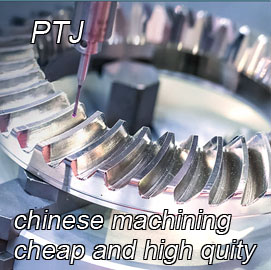
нашите услуги
- 5-осна обработка
- Cnc фрезоване
- Cnc завъртане
- Обработващи индустрии
- Процес на обработка
- Повърхностна обработка
- Обработка на метали
- Обработка на пластмаса
- Мухъл за прахова металургия
- Леене под налягане
- Галерия с части
Казуси
- Авто метални части
- Машинни части
- LED радиатор
- Сградни части
- Мобилни части
- Медицински части
- Електронни части
- Персонализирана обработка
- Части за велосипеди
Списък с материали
- Обработка на алуминий
- Титанова обработка
- Механична обработка от неръждаема стомана
- Медна обработка
- Месингова обработка
- Механична обработка на супер сплави
- Погледнете машинна обработка
- UHMW механична обработка
- Унилатна механична обработка
- PA6 Механична обработка
- PPS механична обработка
- Тефлонова обработка
- Обработка на инконел
- Обработка на инструментална стомана
- Още материал
Галерия с части