Изчерпателно ръководство за това как да настроите режещ инструмент за струг
Настройването на режещ инструмент за струг е основно умение за всеки машинист, особено когато работите със струговащи машини с компютърно цифрово управление (CNC). Правилната настройка на инструмента е от решаващо значение за постигане на прецизни и точни резултати от обработката. В това изчерпателно ръководство ще се задълбочим в сложните подробности за това как да настроите режещ инструмент за струг за CNC струговане. От основите на компонентите на инструмента за струг до усъвършенствани техники за оптимизиране на производителността на рязане, тази статия има за цел да предостави цялостно разбиране на процеса. До края на това ръководство ще имате необходимите знания и умения, за да настроите режещ инструмент за струг с увереност и прецизност, осигурявайки оптимални резултати във вашите CNC операции по струговане.
Разбиране на режещите инструменти за струг
В света на машинната обработка режещите инструменти за стругове са незаменими компоненти за оформяне и трансформиране на суровини в прецизно проектирани части. Независимо дали работите с традиционни ръчни стругове или усъвършенствани машини за струговане с ЦПУ, задълбоченото разбиране на режещите инструменти за стругове е от съществено значение. В този раздел ще се задълбочим в характеристиките, функциите и видовете режещи инструменти за струг.
Характеристики на режещите инструменти за стругове
Режещите инструменти за стругове са предназначени за извършване на различни операции по обработка, като струговане, облицовка, нарязване на канали, нарязване на резба и др. Тези инструменти имат няколко общи характеристики:
- Твърдост: Режещите инструменти за стругове обикновено са изработени от бързорежеща стомана (HSS), карбид или други специализирани материали за инструменти. Тези материали са избрани заради тяхната твърдост, позволяваща на инструмента да издържа на високите температури и налягания, генерирани по време на рязане.
- Режещ ръб: Режещият ръб на инструмента за струг е частта, която действително премахва материала от детайла. Той е проектиран да бъде остър и прецизен, а геометрията на режещия ръб може да варира в зависимост от конкретната задача, за която е предназначен инструментът.
- Опашка: Стъблото на инструмента за струг е частта, която се затяга в държача на инструмента. Осигурява стабилност и твърдост на инструмента по време на процес на обработка. Дизайнът на опашката може да се различава в зависимост от типа инструмент и спецификациите на производителя.
- Държач за инструмент: Държачът на инструмента е ключов компонент, особено при струговане с ЦПУ, тъй като държи сигурно инструмента на струга на място. Той трябва да осигурява стабилност, прецизност и лекота на настройка, за да осигури оптимална работа на инструмента.
- геометрия: Геометрията на режещия инструмент, включително наклонения ъгъл, ъгъла на хлабина и стружкочупващия инструмент, играе важна роля при определяне на производителността на инструмента. Правилната геометрия е от съществено значение за постигане на ефективно отстраняване на материала и евакуация на стружките.
- покритие: Много режещи инструменти за стругове се предлагат със специализирани покрития, като TiN (титанов нитрид) или TiAlN (титанов алуминиев нитрид), за да се увеличи живота на инструмента, да се намали триенето и да се подобри производителността.
Функции на режещите инструменти за стругове
Режещите инструменти за стругове изпълняват няколко основни функции в процеса на обработка:
- Премахване на материал: Основната функция на режещите инструменти за струг е да отстраняват материал от детайла. Това отстраняване може да стане чрез завъртане (завъртане на детайла по време на рязане), лицево лице (създаване на равна повърхност) или други операции.
- Контрол на размерите: Режещите инструменти са отговорни за гарантирането, че размерите на обработваната част отговарят на желаните спецификации. Прецизният контрол е от съществено значение за постигане на точни и постоянни резултати.
- Обработка на повърхността: Качеството на повърхността се определя от остротата на режещия инструмент, геометрията и използваните параметри на рязане. Добре поддържаният и правилно настроен режещ инструмент допринася за гладка и фина повърхност.
- Контрол на чипове: Ефективният контрол на стружките е от съществено значение за предотвратяване на натрупването на стружки и поддържане на чиста и безопасна работна среда. Стругочупвачът на някои инструменти помага за по-лесното отстраняване на стружките.
- Ефективност: Режещите инструменти за стругове са проектирани да направят процесите на обработка ефективни и рентабилни. Те помагат за минимизиране на материалните отпадъци и оптимизират живота на инструмента, намалявайки производствените разходи.
Видове режещи инструменти за стругове
Режещите инструменти за стругове се предлагат в различни типове, всеки от които е пригоден за специфични задачи за обработка. Ето някои често срещани типове:
- Инструменти за струговане: Тези инструменти са универсални и се използват за операции на цилиндрично струговане. Те могат да оформят външните и вътрешните повърхности на детайла.
- Пробивни инструменти: Пробивните инструменти се използват за разширяване или завършване на съществуващи дупки. Те са проектирани за прецизност и точност при обработката на отвори.
- Инструменти за разделяне: Инструментите за разделяне се използват за отделяне на детайл от по-голям материал. Те създават дефинирани разделителни линии с минимални отпадъци.
- Инструменти за нишки: Инструментите за нарязване на резби се използват за нарязване на резби върху детайл. Предлагат се в различни форми и размери за различни изисквания за резби.
- Инструменти за нарязване: Инструментите за нарязване създават жлебове или вдлъбнатини върху детайла, обикновено за поставяне на О-пръстени, задържащи пръстени или други елементи.
- Облицовъчни инструменти: Облицовъчните инструменти са предназначени за създаване на плоски повърхности в края на детайла. Те често се използват за постигане на перпендикулярни повърхности или отстраняване на материал от края на детайла.
Разбирането на характеристиките и функциите на режещите инструменти за струг е от съществено значение за избора на правилния инструмент за конкретна задача за обработка. Изборът на режещ инструмент може значително да повлияе на качеството и ефективността на процеса на обработка, което го прави критично решение при всяка операция на струг. Освен това правилната поддръжка и настройка на инструмента са жизненоважни за осигуряване на последователни и прецизни резултати, които ще бъдат обсъдени по-подробно по-късно в това ръководство.
Видове режещи инструменти за стругове
Режещите инструменти за стругове се предлагат в различни типове, всеки от които е специално проектиран за определена задача за обработка. Разбирането на тези различни видове режещи инструменти и техните приложения е от съществено значение за избора на правилния инструмент за дадена работа. Ето някои често срещани видове режещи инструменти за струг:
Инструменти за струговане:
- Инструмент с кръгъл нос: Използва се за стругови операции с общо предназначение. Той разполага със заоблен режещ ръб и е подходящ както за груби, така и за довършителни срезове.
- Диамантен инструмент: Наречен заради режещия си ръб с форма на диамант, той е идеален за прецизна обработка на различни материали, включително метали и пластмаси.
- Инструмент с квадратен нос: Разполага с квадратен режещ ръб и обикновено се използва за операции по лицево и раменно завъртане.
Пробивни инструменти:Вътрешна скучна лента: Използва се за уголемяване и завършване на съществуващи отвори в детайла. Той е проектиран за прецизност и може да създаде точни вътрешни размери.
Инструменти за разделяне:Разделително острие: Тези инструменти се използват за отрязване на детайл от по-голям материал. Те създават дефинирана разделителна линия с минимални отпадъци.
Инструменти за нишки:
- Инструмент за рязане на резба: Предназначен за създаване на външни резби върху детайл. Предлагат се в различни форми и размери за различни изисквания за резби.
- Инструмент за преследване на нишки: Използва се за преследване или възстановяване на съществуващи нишки. Тези инструменти обикновено се използват за ремонт на резби.
Инструменти за нарязване:Инструмент за нарязване: Тези инструменти създават жлебове или вдлъбнатини върху детайла, често за поставяне на О-пръстени, задържащи пръстени или други елементи.
Облицовъчни инструменти:Инструмент за облицовка: Използва се за създаване на плоски повърхности в края на детайла. Често се използва за постигане на перпендикулярни повърхности или отстраняване на материал от края на детайла.
Инструменти за разделяне и нарязване:Инструмент за комбиниране: Тези многофункционални инструменти са проектирани както за операции на разделяне, така и за нарязване, спестявайки време и смяна на инструменти.
Инструменти за резбоване и нарязване на канали:Инструмент за комбиниране на резби и канали: Идеален за задачи, които изискват операции както за нарязване на резби, така и за нарязване на канали върху един и същ детайл.
Инструменти за скосяване:Инструмент за скосяване: Използва се за създаване на фаски или скосени ръбове върху детайла. Фаските често се прилагат за подобряване на външния вид и лесно сглобяване на обработени части.
Инструменти за нарязване:Инструмент за нарязване: Набраздяването е процес на създаване на текстуриран модел върху детайла, обикновено за подобрено сцепление или естетика. Инструментите за нарязване се предлагат в различни модели и дизайни.
Инструменти за формоване:Инструмент за формуляр: Тези инструменти са специално проектирани за специфични геометрии на части, често използвани за производство на сложни и нестандартни форми.
Специални инструменти:Инструменти за профили: Използва се за създаване на сложни профили върху детайл.
Инструменти за облицоване и струговане: Те са предназначени както за лицеви, така и за стругови операции.
Инструменти за рязане: Проектиран за рязане на детайла за създаване на отделни части или отстраняване на излишния материал.
Изборът на правилния режещ инструмент зависи от фактори като материала, който се обработва, желаното покритие, необходимите размери и конкретната операция, която се извършва. От съществено значение е да изберете подходящия инструмент и да го поддържате правилно, за да осигурите ефективна и точна обработка. Правилният избор на инструмент, заедно с правилната настройка и настройка, е от решаващо значение за постигане на висококачествени резултати при операции на струг.
Компоненти на режещ инструмент за струг
Режещият инструмент за струг е прецизен инструмент, предназначен за оформяне, рязане и отстраняване на материал от детайл. За да разберете как работи и как правилно да го настроите, е изключително важно да сте запознати с различните му компоненти. Ето основните компоненти на режещия инструмент за струг:
- Държач за инструмент:Държачът на инструмента е частта, която закрепва режещия инструмент на място. Прикрепя се към стойката на инструмента на струга и осигурява необходимата твърдост и стабилност за операции по обработка. Държачите за инструменти се предлагат в различни дизайни, за да поберат различни видове режещи инструменти.
- Опашка:Стъблото е частта от режещия инструмент, която пасва в държача на инструмента. Обикновено е цилиндричен и е здраво захванат в държача. Размерите и формата на стеблото може да варират в зависимост от типа и дизайна на инструмента.
- Режещ ръб:Режещият ръб е острата част на инструмента, която влиза в контакт и премахва материала от детайла. Качеството на режещия ръб и неговата геометрия значително влияят върху производителността на рязане и покритието на повърхността. Важно е да поддържате остротата и прецизността на режещия ръб.
- Поставете:Много съвременни режещи инструменти използват сменяеми вложки, които обикновено са направени от твърди материали като карбид или керамика. Тези вложки имат режещата геометрия и са закрепени в джоб на режещия инструмент. Те могат да се завъртат или сменят, когато се износят или повредят, което удължава живота на инструмента.
- Нос на инструмента:Върхът на инструмента е самият връх на режещия инструмент, където режещият ръб и вложката (ако се използва) се събират. Върхът на инструмента трябва да бъде точно позициониран и подравнен за прецизна обработка. Някои режещи инструменти за струг имат регулируем радиус на върха на инструмента за по-добър контрол върху работата на инструмента.
- Инструмент фланг:Страничната повърхност на инструмента е страничната повърхност на режещия инструмент, която не е част от режещия ръб. Правилните ъгли на хлабина на страната на инструмента осигуряват евакуация на стружките и намаляват триенето между инструмента и детайла.
- Лице на инструмента:Наклонената повърхност е повърхността на режещия инструмент, която е обърната към детайла. Ъгълът и състоянието на наклонената повърхност влияят върху образуването на стружки и ефективността на процеса на рязане. Наклоненият ъгъл е критичен аспект от геометрията на инструмента.
- Ъгъл на облекчение на инструмента:Релефният ъгъл е ъгълът между страната на инструмента и оста на инструмента. Той гарантира, че режещият ръб не се трие в детайла, намалявайки триенето и генерирането на топлина.
- Ъгъл на свободния инструмент:Ъгълът на хлабина е ъгълът между наклонената повърхност и повърхността на детайла. Той позволява на стружките да текат гладко и предотвратява намесата между инструмента и детайла.
- Чип разбивач (ако е приложим):Някои режещи инструменти, особено тези, използвани за груби операции, имат стружкочупвач, жлеб или прорез на наклонената повърхност. Стружкочупачката помага за контролиране на образуването на стружки и подобряване на евакуацията на стружки.
Правилното сглобяване, подравняване и поддръжка на тези компоненти са от съществено значение за постигане на прецизна и ефективна обработка. Изборът на режещ инструмент и неговата настройка трябва да бъдат съобразени с конкретната операция на обработка и материала, върху който се работи. Редовната проверка и поддръжка на компонентите на режещия инструмент също са необходими, за да се осигурят постоянни и висококачествени резултати.
Избор на правилния режещ инструмент за работата
Изборът на правилния режещ инструмент е критично решение при всяка машинна операция, тъй като значително влияе върху качеството, ефективността и прецизността на работата. При избора на подходящия режещ инструмент за конкретна работа трябва да се имат предвид няколко фактора. Ето ръководство за това как да изберете правилния режещ инструмент за вашия проект за обработка:
1. Материал на детайла:
Материалът, който обработвате, е един от най-критичните фактори при избора на инструмент. Различните материали имат различна твърдост, топлопроводимост и абразивност. Помислете за следното:
- Твърдост: Твърдите материали като закалена стомана или керамика изискват режещи инструменти с твърди режещи ръбове, като карбидни пластини, за да издържат на високите сили на рязане.
- Меки материали: За по-меки материали като алуминий или пластмаса може да са достатъчни бързорежеща стомана (HSS) или други инструменти.
2. Операция по обработка:
Конкретната операция, която извършвате, като струговане, фрезоване, пробиване, нарязване на резби или канали, ще диктува вида на режещия инструмент, от който се нуждаете. Различните инструменти са предназначени за различни задачи и изборът на правилния гарантира оптимална производителност.
3. Скорост на рязане и скорост на подаване:
Определете необходимата скорост на рязане и скорост на подаване въз основа на материала и операцията на обработка. Производителите на режещи инструменти предоставят препоръки за тези параметри въз основа на дизайна на инструмента и материала, който се обработва. Спазването на тези препоръки е изключително важно за постигане на желаните резултати.
4. Геометрия на инструмента:
Помислете за геометрията на режещия инструмент, включително наклонения ъгъл, ъгъла на хлабина и радиуса на върха на инструмента. Геометрията на инструмента трябва да съответства на материала и вида на рязане. Например положителен наклонен ъгъл е подходящ за по-меки материали, докато отрицателен наклонен ъгъл е по-добър за по-твърди материали.
5. Размери на детайла:
Размерът и размерите на детайла също влияят върху избора на инструмент. Някои режещи инструменти са по-подходящи за груби операции за бързо отстраняване на насипен материал, докато други са проектирани за довършителни работи за постигане на прецизни размери и повърхностни покрития.
6. Изисквания за повърхностно покритие:
Ако имате нужда от специфично покритие на повърхността, изберете режещ инструмент с подходяща геометрия и острота. Инструментите за довършителни работи са проектирани да осигурят по-гладка повърхност, докато инструментите за груба обработка са по-ефективни за отстраняване на материал.
7. Материал на инструмента:
Изборът на материал за инструмента е от решаващо значение. Инструментите от твърд сплав, бързорежеща стомана (HSS), керамика и инструменти с покритие имат своите предимства и ограничения. Вземете предвид фактори като живот на инструмента, устойчивост на износване и цена на материала на инструмента при вашето решение.
8. Охлаждаща течност и смазка:
Помислете дали операцията по рязане изисква охлаждаща течност или смазка. Някои материали генерират прекомерна топлина по време на машинна обработка и използването на правилната охлаждаща течност или смазка може да удължи живота на инструмента и да подобри ефективността на рязане.
9. Покрития за инструменти:
Много съвременни режещи инструменти се предлагат със специализирани покрития като TiN (титанов нитрид) или TiAlN (титанов алуминиев нитрид) за подобряване на устойчивостта на износване и намаляване на триенето. Изберете инструмент с подходящо покритие за вашето конкретно приложение.
10. Съображения за разходите:
Балансирането на цената на режещия инструмент с неговата производителност и дълголетие е от решаващо значение. Въпреки че първокласните инструменти могат да предложат по-дълъг живот на инструмента и по-добра производителност, важно е да намерите баланс, който да съответства на бюджета на вашия проект.
11. Съвместимост на държача и машината:
Уверете се, че избраният режещ инструмент е съвместим с инструментодържащата система на вашия струг или обработващ център. Държачът на инструмента трябва да осигурява стабилност и твърдост на режещия инструмент по време на процеса на обработка.
В крайна сметка правилният режещ инструмент за работата ще зависи от комбинация от тези фактори. Винаги се консултирайте с препоръките на производителя на инструмента и обмислете да потърсите съвет от опитни машинисти или експерти по инструментите, ако не сте сигурни. Правилният избор и настройка на инструмента са основни за постигане на ефективни и прецизни резултати от обработката.
Настройка на инструмента за рязане на струг
Настройването на режещ инструмент за струг за CNC струговане е систематичен процес, който включва няколко ключови стъпки. Всяка стъпка е жизненоважна, за да се гарантира, че режещият инструмент е правилно позициониран и подравнен, което в крайна сметка води до прецизна и ефективна обработка. Нека преминем през процеса стъпка по стъпка:
Стъпка 1: Подготовка на струга и детайла
Преди да можете да настроите режещия инструмент, важно е да подготвите както струга, така и детайла:
- Закрепете детайла: Уверете се, че детайлът е здраво захванат в патронника или цангата на струга. Уверете се, че се върти гладко, без никакво трептене или вибрации.
- Безопасност: Уверете се, че всички мерки за безопасност са налице, включително използването на подходящи лични предпазни средства (PPE) и правилните настройки на струга.
Стъпка 2: Избор на правилния държач за инструменти
Държачът на инструмента е критичен компонент в процеса на настройка. Изберете подходящия държач за инструменти въз основа на фактори като вида на режещия инструмент, извършваната операция и системата за закрепване на инструмента на струга.
- Съпоставете държача на инструмента с режещия инструмент: Уверете се, че държачът на инструмента е съвместим с вида и размера на режещия инструмент, който възнамерявате да използвате.
- Твърдост на държача на инструмента: Изберете държач за инструменти, който осигурява стабилност и твърдост. Това е особено важно при приложения с висока точност.
Стъпка 3: Монтиране на режещия инструмент
Монтирането на режещия инструмент включва закрепването му в държача на инструмента и гарантирането, че е стабилно и правилно позициониран:
- Закрепете режещия инструмент: Поставете режещия инструмент в държача на инструмента и затегнете всички затягащи механизми, като фиксиращи винтове или цанги. Уверете се, че инструментът се държи здраво.
- Ориентация: Уверете се, че режещият инструмент е ориентиран правилно по отношение на детайла. Инструментът трябва да бъде позициониран така, че да захваща детайла под желания ъгъл и дълбочина.
Стъпка 4: Регулиране на височината на инструмента и централната линия
Правилната височина на инструмента и подравняването на централната линия са от решаващо значение за постигане на прецизни размери на обработка:
- Регулиране на височината на инструмента: Регулирайте височината на инструмента, за да го подравните с централната линия на шпиндела на струга. Използвайте уред за измерване на височината на инструмента или тестова лента, за да настроите инструмента на правилната височина.
- Подравняване на централната линия: Уверете се, че инструментът е подравнен с централната линия на шпиндела на струга. Несъответствието може да доведе до машинна обработка извън центъра, което засяга точността на детайла.
Стъпка 5: Задаване на компенсация на радиуса на върха на инструмента
За CNC струговане, компенсацията на радиуса на върха на инструмента отчита геометрията на режещия инструмент. Това е особено важно, когато използвате инструменти за вмъкване:
- Определете радиуса на върха на инструмента: Измерете или потърсете точния радиус на носа на вложката на режещия инструмент, която използвате.
- Въведете стойността на радиуса: В софтуера за управление на CNC въведете измерената стойност на радиуса на върха на инструмента, за да сте сигурни, че машината компенсира геометрията на инструмента при обработка.
Стъпка 6: Задаване на отмествания на инструмента
Отместванията на инструмента отчитат вариациите в размерите на инструмента и геометрията на детайла. Те гарантират, че позицията на инструмента е точно регулирана за обработка:
- Изберете правилното отместване на инструмента: Определете подходящата стойност на отместването на инструмента въз основа на геометрията на инструмента и операцията по обработка. Тази стойност на компенсиране компенсира всички несъответствия.
- Въведете стойности на отместване: Въведете избраните стойности на отместване в софтуера за управление на ЦПУ. Тези стойности ще инструктират машината как да регулира точно позицията на инструмента.
По време на процеса на настройка на инструмента използвайте прецизни измервателни инструменти като микрометри, ръстомери и индикатори за циферблат, за да проверите и фино регулирате подравняването на инструмента. Редовно проверявайте и поддържайте режещия инструмент, за да сте сигурни, че остава остър и в добро състояние, тъй като добре поддържаният инструмент допринася за постоянни и точни резултати от обработката.
Правилното настройване на режещия инструмент за струг в тези стъпки е от решаващо значение за постигане на оптимални резултати при CNC струговане. Прецизността и вниманието към детайлите по време на настройката на инструмента са ключови фактори за производството на висококачествени машинни части.
Оптимизиране на параметрите на рязане за CNC струговане
Оптимизирането на параметрите на рязане е от съществено значение за постигане на ефективни и висококачествени CNC стругови операции. Четирите ключови аспекта, които трябва да се имат предвид при оптимизиране на параметрите на рязане, са скорости и подавания, дълбочина на рязане, режещи течности и смазочни материали и управление на живота на инструмента.
1. Скорости и емисии:
- а. Скорост на рязане (скорост на повърхността):Скоростта на рязане, често наричана повърхностна скорост, е скоростта, с която детайлът и режещият инструмент взаимодействат. Измерва се в повърхностни футове за минута (SFM) или метри за минута (m/min). За да оптимизирате скоростта на рязане, вземете предвид материала, който се обработва, и материала на инструмента. Инструментите за бързорежеща стомана (HSS) имат по-ниски препоръчителни скорости на рязане от твърдосплавните инструменти, например. Консултирайте се с данните на производителя на инструмента или наръчниците за обработка, за да определите препоръчителните скорости на рязане за конкретни материали и инструменти.
- b. Скорост на подаване:Скоростта на подаване е линейната скорост, с която режещият инструмент напредва в детайла. Измерва се в инчове на оборот (IPR) или милиметри на оборот (mm/rev). За да оптимизирате скоростта на подаване, вземете предвид фактори като свойства на материала, геометрия на инструмента и желаното покритие на повърхността. По-високите скорости на подаване обикновено са по-продуктивни, но може да изискват по-здрави инструменти.
- ° С. Връзка скорост на рязане и скорост на подаване:Балансирането на скоростта на рязане и скоростта на подаване е от решаващо значение за ефективното отстраняване на материала. Увеличаването на скоростта на рязане обикновено позволява по-висока скорост на подаване, но двете трябва да се регулират заедно, за да се предотврати износването и прегряването на инструмента.
2. Дълбочина на рязане:
- а. Дълбочина на рязане (DOC):Дълбочината на рязане е разстоянието, на което режещият инструмент прониква в детайла. От съществено значение е да вземете предвид материала и възможностите на инструмента. Оптимизирайте дълбочината на рязане въз основа на твърдостта на материала и здравината и твърдостта на инструмента. Плитки срезове може да са необходими за по-твърди материали, докато по-дълбоки срезове могат да бъдат постигнати за по-меки материали.
- b. Аксиална и радиална дълбочина на рязане:При CNC струговане вземете предвид както аксиалната (по дължината на детайла), така и радиалната (по диаметъра на детайла) дълбочина на рязане. Оптималните дълбочини за всеки ще варират в зависимост от операцията и материала.
3. Режещи течности и смазки:
- а. Избор на правилната течност за рязане:Течностите за рязане са от съществено значение за разсейване на топлината, намаляване на триенето и подобряване на евакуацията на стружките. Изберете подходящата течност за рязане въз основа на материала и операцията по обработка. Водоразтворимата охладителна течност, базираната на минерално масло или синтетичната охлаждаща течност могат да бъдат предпочитани за различни материали.
- b. Правилно приложение:Нанесете ефективно режещи течности върху зоната на рязане, за да осигурите адекватно смазване и охлаждане. Това може да бъде направено чрез наводнено охлаждане, системи за мъгла или подаване на охлаждаща течност през инструмента, в зависимост от възможностите на машината.
- ° С. Мониторинг и поддръжка:Редовно наблюдавайте нивата, състоянието и замърсяването на флуида за рязане, за да сте сигурни, че остават ефективни. Поддържайте системите за флуиди за рязане, за да предотвратите проблеми като бактериален растеж и разграждане.
4. Управление на живота на инструмента:
- а. Проверка и поддръжка на инструмента:Прилагайте рутинна програма за проверка и поддръжка на инструменти, за да сте сигурни, че инструментите са в добро състояние. Тъпите или повредени инструменти могат да доведат до лошо качество на обработка и намален живот на инструмента.
- b. График за подмяна на инструменти:Създайте график за смяна на инструменти въз основа на фактори като износване на инструмента, време за работа на машината и производствени изисквания. Това помага за предотвратяване на неочаквани повреди на инструмента и поддържа постоянно качество на обработка.
- ° С. Оптимизиране на живота на инструмента:Някои материали и покрития за инструменти предлагат по-дълъг живот на инструмента. Обмислете използването на високопроизводителни инструменти, за да оптимизирате живота на инструмента и да намалите времето за престой в производството.
- д. Контрол на чипа на инструмента:Ефективният контрол на стружки, включително използването на стругочупачи и подходяща геометрия на инструмента, може да удължи живота на инструмента чрез намаляване на износването, причинено от стружки.
Оптимизирането на параметрите на рязане при CNC струговане е непрекъснат процес. Може да се наложи експериментиране и фина настройка, за да се намерят най-добрите параметри за конкретно приложение. Редовно наблюдавайте и коригирайте тези параметри, за да осигурите оптимална производителност на обработката, живот на инструмента и качество на частта. Правилно оптимизираните параметри на рязане не само подобряват ефективността на машинната обработка, но също така намаляват износването на инструмента и в крайна сметка производствените разходи.
Отстраняване на често срещани проблеми в настройката на инструмента
Отстраняването на често срещани проблеми при настройката на инструмента е основно умение за машинистите и CNC операторите. Разбирането и справянето с тези проблеми може да помогне за поддържане на прецизността и качеството на машинните операции. Ето някои често срещани проблеми с настройката на инструмента и техните решения:
1. Бърморене с инструменти:
Проблем: Тракането на инструмента възниква, когато режещият инструмент вибрира по време на процеса на обработка, което води до лошо покритие на повърхността, износване на инструмента и потенциална повреда на детайла.
Решение:
- Намалете скоростта или увеличете подаването: Регулирайте параметрите на рязане, като намалите скоростта на рязане или увеличите скоростта на подаване. Тази промяна може да смекчи вибрациите и да намали бърборенето.
- Проверете твърдостта на инструмента: Уверете се, че държачът и инструментът са правилно закрепени и че инструментът не се простира твърде далеч от държача.
- Проверете затягането на детайла: Уверете се, че детайлът е здраво захванат, за да предотвратите вибрации, свързани с детайла.
- Използвайте техники за овлажняване: Някои машини се предлагат с функции за потискане на вибрациите. Ако има такива, обмислете използването им.
- Изберете по-твърд инструмент: По-твърд инструмент, като такъв с по-малко жлебове, може да помогне за намаляване на бърборенето.
2. Лошо покритие на повърхността:
Проблем: Лошото покритие на повърхността може да е резултат от проблеми с настройката на инструмента или параметрите на рязане, което води до грапави или неравномерни повърхности на детайла.
Решение:
- Проверка на геометрията на инструмента: Уверете се, че геометрията на режещия инструмент е подходяща за операцията. Остър инструмент с правилна геометрия е от решаващо значение за постигане на добро покритие на повърхността.
- Оптимизиране на параметрите на рязане: Регулирайте скоростта на рязане, скоростта на подаване и дълбочината на рязане, за да намерите най-добрата комбинация за конкретния материал и операция.
- Проверка за износване на инструмента: Проверете инструмента за признаци на износване или повреда, като натрошени ръбове. Сменете или шлайфайте отново инструмента, ако е необходимо.
- Използвайте подходяща течност за рязане: Правилното смазване и охлаждане може значително да повлияе на покритието на повърхността. Използвайте правилната течност за рязане за материала и операцията.
- Минимизиране на вибрациите: Обърнете внимание на проблемите с вибрациите, за да избегнете създаването на повърхностни неравности.
3. Неточности в размерите:
Проблем: Частите може да имат неправилни размери поради неправилно подравнени инструменти или износване на инструмента.
Решение:
- Проверете настройката на инструмента: Уверете се, че инструментът е правилно настроен с правилната височина и подравняване по отношение на детайла.
- Калибриране на машината: Уверете се, че CNC машината е правилно калибрирана и че интерпретира точно отместванията на инструмента и данните за инструмента.
- Коригирайте отместванията на инструмента: Коригирайте всички грешки в отместванията на инструмента чрез точно измерване на инструмента и въвеждане на правилните стойности на отместване в CNC управлението.
- Проверете износването на инструмента: Редовно проверявайте режещия инструмент за износване и го сменете или шлифовайте отново, когато е необходимо.
4. Проблеми с контрола на чипа:
Проблем: Неправилният контрол на стружки може да доведе до проблеми като запушване на стружки, лошо извеждане на стружки и повреда на детайла или инструмента.
Решение:
- Изберете правилната геометрия на инструмента: Изберете режещ инструмент с подходящ стружколомач или геометрия за материала и работата.
- Оптимизиране на параметрите на рязане: Регулирайте скоростите на подаване, скоростите на рязане и дълбочините на рязане, за да оптимизирате образуването и евакуацията на стружките.
- Използвайте подходящо смазване: Правилното използване на флуиди за рязане може да помогне за смазване и да улесни евакуацията на стружките.
- Проверете подравняването на инструмента и детайла: Уверете се, че инструментът е правилно подравнен с детайла, за да предотвратите проблеми, свързани със стружките.
5. Счупване на инструмента:
Проблем: Счупването на инструмента може да възникне поради прекомерна сила, неправилна настройка на инструмента или проблеми, свързани с материала.
Решение:
- Оптимизиране на параметрите на рязане: Намалете силите на рязане чрез регулиране на параметри като скорости на подаване, скорости на рязане и дълбочини на рязане.
- Проверете настройката на инструмента: Уверете се, че инструментът е здраво монтиран в държача на инструмента и че е правилно подравнен.
- Използвайте подходящ инструментален материал: Изберете правилния инструментален материал за конкретния материал, който обработвате. Например, карбидните инструменти са по-добри за твърди материали.
- Проверете за износване на инструмента: Редовно проверявайте инструмента за признаци на износване и го сменете, преди да стане прекалено износен и податлив на счупване.
Справянето с тези често срещани проблеми с настройката на инструмента изисква комбинация от подходящо обучение, редовна поддръжка и систематичен подход за отстраняване на неизправности. Способността за диагностициране и разрешаване на проблеми, свързани с инструментите, е от решаващо значение за постигане на висококачествени и ефективни резултати от обработката.
В заключение
Процесът на настройка и оптимизиране на режещи инструменти за стругове за CNC струговане е решаващ аспект от машинната обработка, който значително влияе върху качеството, ефективността и прецизността на производствените процеси. Дълбокото разбиране на компонентите и функциите на режещите инструменти, както и факторите, включени в избора на инструменти, е от съществено значение за машинистите и CNC операторите.
Правилното настройване на режещ инструмент включва систематичен подход, от подготовката на струга и детайла до избора на правилния държач на инструмента, монтирането на инструмента, регулирането на височината на инструмента и подравняването на централната линия и конфигурирането на компенсацията на радиуса на върха на инструмента и отместванията на инструмента. Всяка стъпка играе ключова роля за постигането на прецизни и ефективни резултати от машинната обработка.
Оптимизирането на параметрите на рязане, включително скорости и подавания, дълбочина на рязане, флуиди за рязане и управление на живота на инструмента, е друг критичен аспект на CNC струговането. Чрез внимателно избиране на правилните параметри, машинистите могат да подобрят производителността, да поддържат дълготрайността на инструмента и да подобрят качеството на повърхността.
И накрая, възможността за отстраняване на често срещани проблеми с настройката на инструмента, като тракане на инструмента, лошо покритие на повърхността, неточности на размерите, проблеми с контрола на стружки и счупване на инструмента, е от съществено значение за поддържане на постоянни и висококачествени резултати от обработката. Идентифицирането на тези проблеми и прилагането на подходящи решения гарантира, че процесът на обработка остава плавен и ефективен.
Като цяло, цялостното разбиране на инструментите за рязане на струг и тяхната настройка, съчетано със способността за оптимизиране на параметрите на рязане и отстраняване на проблеми, дава възможност на машинистите да постигнат най-добри резултати при CNC струговане. Непрекъснатото обучение, обучение и опит са ключови за усъвършенстването на тези умения и осигуряването на успешни процеси на обработка.
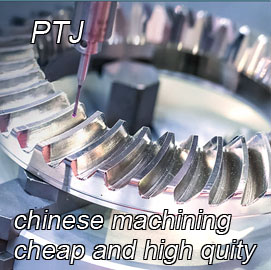
- 5-осна обработка
- Cnc фрезоване
- Cnc завъртане
- Обработващи индустрии
- Процес на обработка
- Повърхностна обработка
- Обработка на метали
- Обработка на пластмаса
- Мухъл за прахова металургия
- Леене под налягане
- Галерия с части
- Авто метални части
- Машинни части
- LED радиатор
- Сградни части
- Мобилни части
- Медицински части
- Електронни части
- Персонализирана обработка
- Части за велосипеди
- Обработка на алуминий
- Титанова обработка
- Механична обработка от неръждаема стомана
- Медна обработка
- Месингова обработка
- Механична обработка на супер сплави
- Погледнете машинна обработка
- UHMW механична обработка
- Унилатна механична обработка
- PA6 Механична обработка
- PPS механична обработка
- Тефлонова обработка
- Обработка на инконел
- Обработка на инструментална стомана
- Още материал